Learn from Industry Experts
Ultra - Low Ice - Core Temperature
Next – Generation Ice Cubes 5cm
Actionable Training
Lorem ipsum dolor sit amet, consectetur adipiscing elit.
Interesting Quizzes
Lorem ipsum dolor sit amet, consectetur adipiscing elit.
Premium Material
Lorem ipsum dolor sit amet, consectetur adipiscing elit.
What Our Clients Have to Say
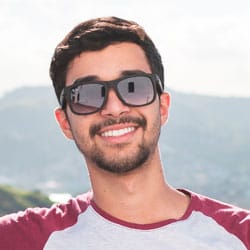
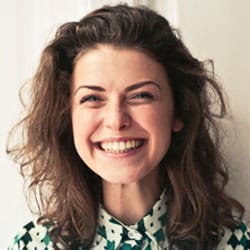
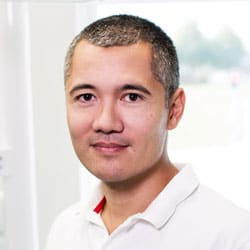
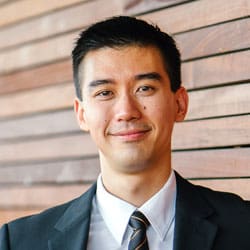
How to order your boxes?
- The process of customizing paper boxes is as follows:
- first, clarify the requirements, including size, material, printed patterns, etc.;
- then communicate the plan and quotation;
- after confirmation, place an order for production,
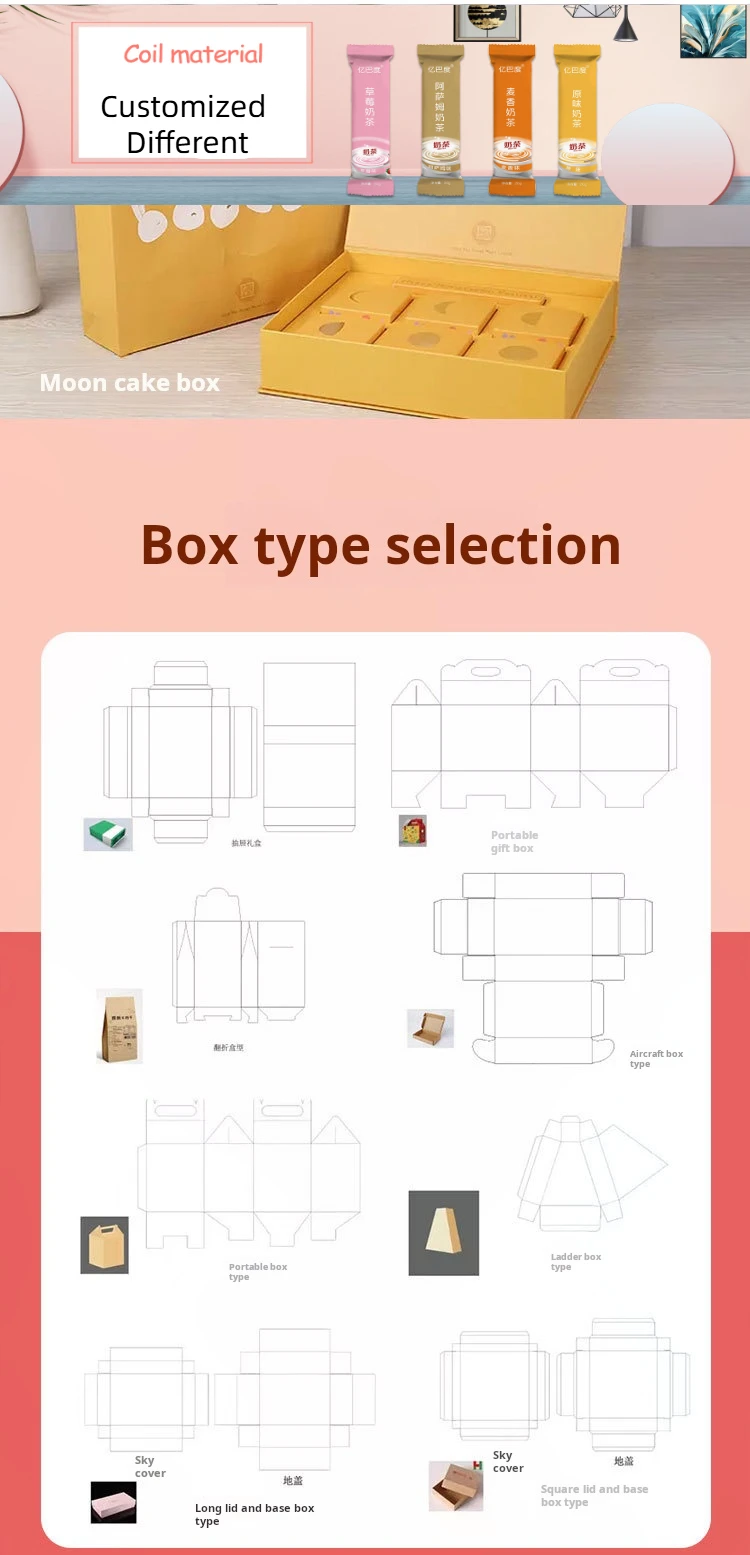
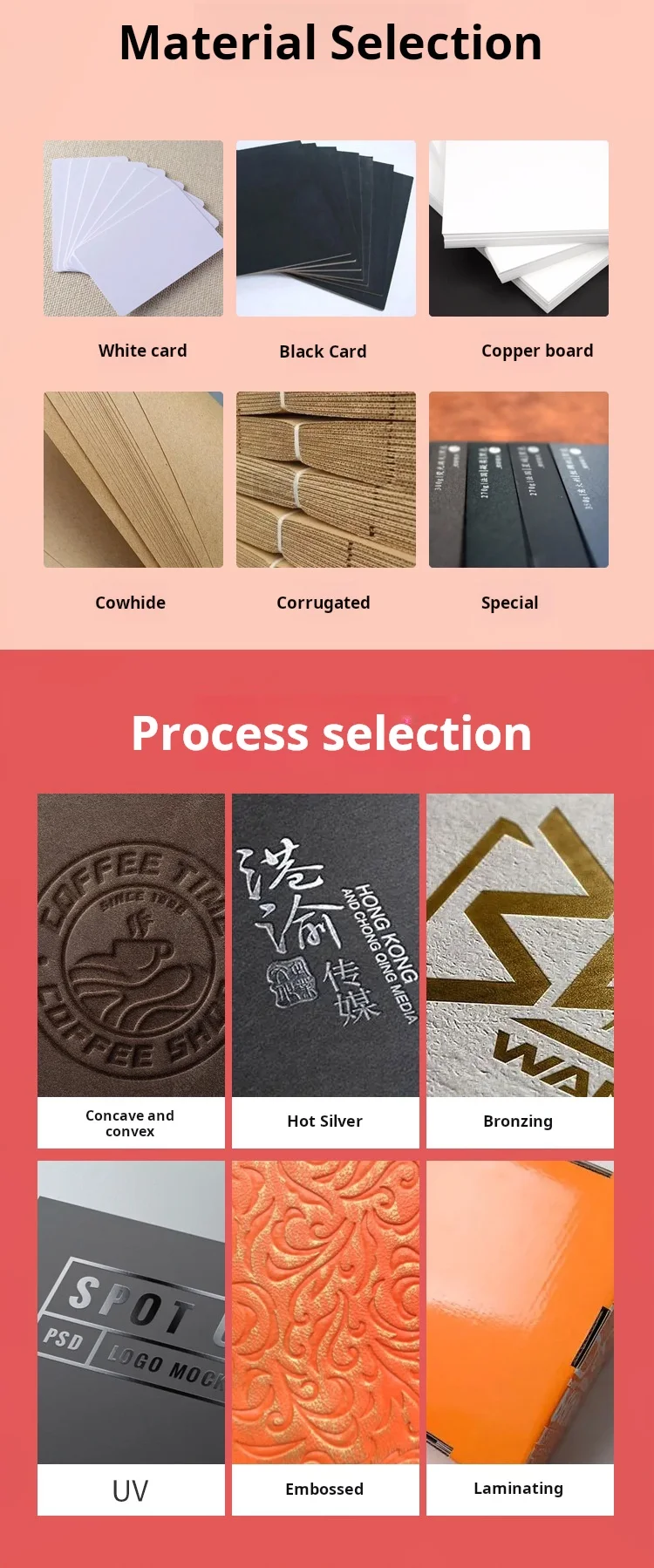
**Core of Quality Control in Carton Production**
Quality control in carton production covers multiple key links.
Raw material selection, production process control, and finished product inspection are all core points. Raw materials are the foundation of carton quality. The grammage, strength, and stiffness of paper are extremely important.
For example, for cartons used to package electronic products, high-strength paper needs to be selected to withstand collisions and squeezes during transportation.
At the same time, the moisture content of cardboard should be strictly controlled. If the moisture content is too high, the carton is prone to deformation; if it is too low, it will become brittle and affect toughness.
In addition, the quality of auxiliary materials such as ink and glue cannot be ignored. Environmentally friendly ink can ensure that cartons meet packaging requirements for industries such as food and pharmaceuticals; high-quality glue ensures the firmness of cartons after forming. Production process is the key to determining carton quality.
In the printing link, accurate color reproduction and clear pattern and text are basic requirements. Advanced printing equipment and processes, such as using CMYK color mode and high-precision printing technology, can avoid color deviation and pattern blurring.
The cutting process needs to ensure accurate dimensions, and the error is controlled within a very small range, otherwise it will lead to a mismatch between the carton and the product.
In the die-cutting process, the sharpness of the blade and pressure control affect the smoothness and forming effect of the carton edge. The pasting process is also important.
Only when the glue is evenly and appropriately applied can the carton be glued and formed without opening glue or thread breakage. Finished product inspection is the last line of defense for quality control. In appearance inspection, check whether the carton surface has defects such as scratches, stains, and wrinkles, and whether the pattern and text are clear and complete.
Dimension measurement requires professional measuring tools to ensure that the length, width, and height of the carton meet the design requirements.
Compression resistance testing simulates transportation and storage environments to test the pressure-bearing capacity of cartons and ensure that products are not crushed during stacking. The folding resistance test evaluates the performance of cartons when folded and used to avoid fracture.
Quality control in carton production requires strict control in all links from raw material selection, production process control to finished product inspection.
Only in this way can high-quality cartons be produced to meet the packaging needs of different products.
I sincerely hope it can help you and make you get better products.